- | 9:00 am
This startup is using robots to 3D print giant wind turbine blades
It will use less material and significantly cut the cost of wind power.
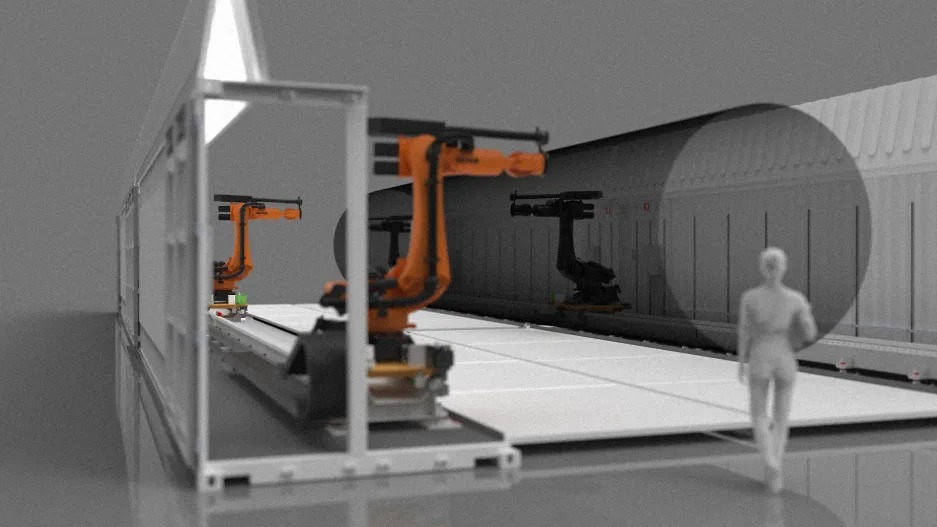
One of the challenges of building a new wind farm is transportation: If a wind turbine blade is 200 feet long, or even longer, it can’t easily travel down highways. In fact, moving a wind turbine can take a year of planning. The video below shows part of the terrifying two-week journey of a single blade up a mountain in China.
The difficulty of delivery pushes up the cost of wind power. But one startup has designed a system to use 3D printing and robotics to manufacture wind turbines in the place where they will be used. “We want to be able to manufacture the foundation, the tower, and the blades all on-site, which is a radical shift from how it’s done today,” says Amolak Badesha, CEO of the startup, called Orbital Composites.
The company developed new tech that allows it to print composite materials at high speeds. Right now, the wind industry uses labor-intensive manufacturing techniques. “Most people don’t know this, but we actually have zero wind blade factories left in the U.S.,” Badesha says. “We used to have more, but they’ve all been offshored because of how manual this process is.” (To qualify for incentives for domestic manufacturing, he says, some companies bring the blades to the U.S. only for sanding and painting.)
Orbital already uses its technology to print drones and satellite parts. To make blades for a wind turbine, it will 3D-print a giant mold, and then print the blade inside the mold. All of the equipment can be delivered to a site in shipping containers.
By eliminating the need to move the final product, it’s easier to make longer blades—and the bigger the blade, the more power a turbine can produce, lowering the cost of energy. Using 3D printing also helps reduce cost. “When you make structures this large, your cost is actually dominated by materials,” says Badesha. “The traditional processes are very wasteful.” By adding only the exact amount of material needed, additive manufacturing eliminates that waste. Reducing the use of material is expected to cut costs by 25%; manufacturing on-site can cut costs by another 10% to 25%.
The engineers are also developing the processes to 3D-print bases and towers for wind turbines. Eventually, the process may also print other components, including magnets that currently rely on rare imported materials, but that could be made domestically. Still, wind blades will come first. In its first demonstration, later this year, the team will print a nearly 30-foot-long wind blade that will be tested for performance.
Next year, in a collaboration with the Department of Energy, it plans to test a 3D-printing robot that can travel back and forth on a cable system as it creates the blades (Badesha likens it to the SkyCam system used with cameras at NFL games). “That allows us to reach the 100-meter-plus [328 feet] scale, which means that we don’t need extensive infrastructure to make these blades,” he says.
The next blade to be tested will be 164 feet long, followed by commercial-scale blades that are nearly as long as a football field. The final product will use recyclable material. (Most current wind-turbine blades aren’t recyclable, though some other manufacturers are now also testing materials that are.) “We’re not only reducing material in the first place, but we’re also going to recycle these materials and reuse them downstream,” Badesha says.