- | 9:00 am
The rise of productization in shaping Saudi Arabia’s next-generation megacities
It’s about setting a new standard for urban development
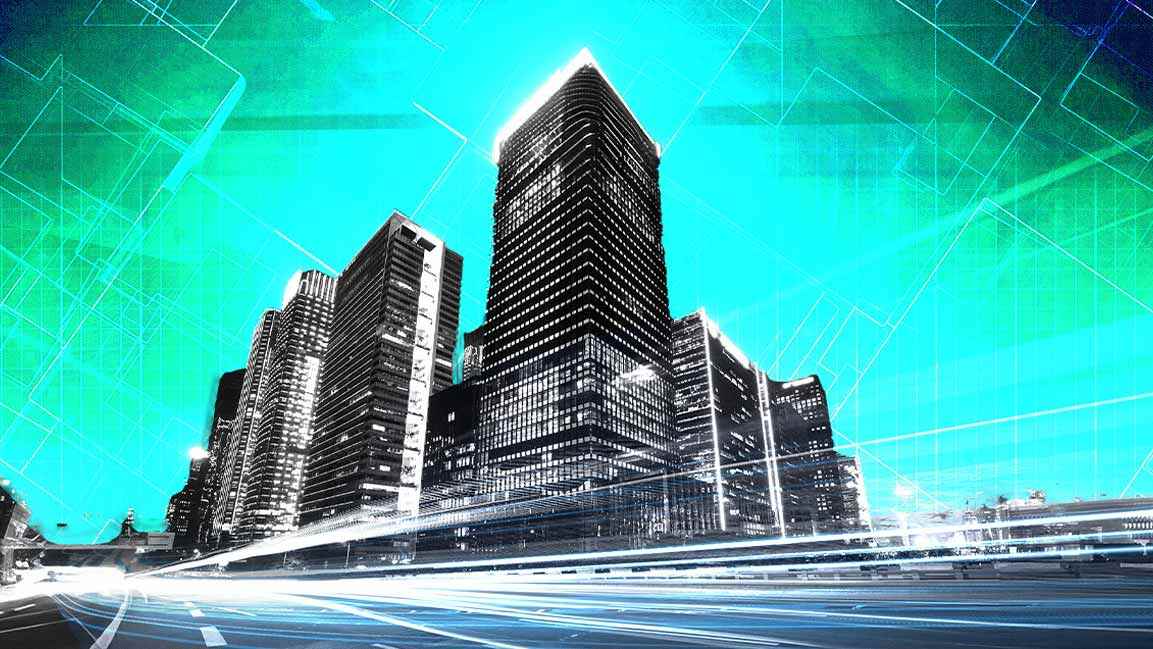
Saudi Arabia’s megacities are rethinking urban development, borrowing a strategy often associated with tech: productization.
This modular, scalable approach treats cities less like sprawling construction sites and more like meticulously designed systems, where each piece is engineered to fit impeccably. The result? Faster timelines, efficient growth, and infrastructure that feels as deliberate as it is ambitious.
Saudi Arabia is betting on cities built with precision—and a touch of pragmatism.
ITS ONLY AN ADVANTAGE
The biggest benefits of using a productized approach in mega-city development are efficiency, scalability, and cost-effectiveness, says Bandar Alkahlan, General Director of the Advanced Manufacturing Technologies Institute at King Abdulaziz City for Science and Technology (KACST). He explains, “By adopting a productized approach, you aim to achieve a standardized, automated production line capable of producing 5,000 housing units per year.”
In Saudi Arabia, where rapid urban expansion is a priority, this approach helps meet the demands of growing cities while maintaining quality. It allows for faster construction timelines, reduced waste, and consistency across large-scale projects, aligning with Vision 2030’s goals of creating affordable and sustainable housing solutions.
Moreover, productization fosters the development of resilient supply chains by sourcing standardized materials and components locally.
Alkahlan believes this enhances economic sustainability and supports local industries and job creation. The consistency achieved through automation reduces dependency on manual labor, thereby minimizing the impact of labor shortages and accelerating urban development projects.
Alkahlan adds, “In the context of Saudi Arabia, this strategy is crucial for meeting the ambitious urban growth plans while maintaining a balance between speed, cost, and quality in the construction process.”
For Daniel Pifko, Chief Product Officer at WakeCap Technologies, the main advantages of productization are speed and risk reduction through better predictability. In Saudi Arabia’s mega-projects, where timelines are tight and the scale is enormous, breaking down the development process into repeatable, modular pieces helps speed up progress.
Pifko adds, “By creating standardized systems and methods, we can build complex structures more efficiently while leaving room for creativity and innovation. It’s a bit like Lego – when you have the pieces ready, building something big doesn’t take as long as it might otherwise.”
ALIGNING TO BUILD SMART, SUSTAINABLE CITIES
Productization inherently supports the concept of smart, sustainable cities by promoting standardization and optimization of resources. By streamlining the construction process through automation and pre-fabrication, productization reduces energy consumption, minimizes waste, and enhances material efficiency.
Additionally, smart manufacturing systems provide data-driven insights, enabling real-time monitoring and better decision-making for sustainability goals. In Saudi Arabia’s urban development context, Alkahlan believes that productization aligns with the vision of integrating smart city technologies while building eco-friendly infrastructure.
Moreover, the emphasis on modular, scalable designs within a productized framework enhances adaptability to environmental changes and urban expansion needs. By incorporating sustainability standards in the design phase, these approaches ensure that buildings and infrastructure can integrate renewable energy solutions, water management systems, and green spaces. This comprehensive planning enables cities to evolve organically while still achieving carbon footprint reduction goals and meeting the broader sustainability targets set by Vision 2030.
Modular and standardized methods are all about predictability, highlights Pifko.
He says, “When you use the same building blocks repeatedly, you reduce the risk of mistakes and delays. It also makes scaling up much easier. Instead of reinventing the wheel every time, you replicate what’s proven to work.”
He adds, “This is especially important in Saudi Arabia, where the scale of development is unlike anything the world has seen. By keeping things consistent, you can expand rapidly without sacrificing quality.”
ADVANCED TECH
KACST is playing a vital role in advancing Saudi Arabia’s construction sector by promoting research and development in automation and smart manufacturing, says Alkahlan.
By supporting initiatives like automated production lines, KACST integrates technologies such as 3D printing, robotics, and modular construction. These technologies enable precise, high-volume production of housing components, improving efficiency and reducing construction time. KACST’s efforts help bridge the gap between innovative research and real-world applications, allowing for the successful transition of these technologies into megacity projects.
Additionally, KACST is focusing on leveraging data analytics, IoT (Internet of Things), and AI-based systems to enhance the monitoring and maintenance of infrastructure within these mega-cities.
These innovations streamline the construction phase and support the long-term sustainability and functionality of the urban environment.
Digital collaboration and data integration are also essential for large-scale projects like Saudi Arabia’s megacities, highlights Pifko.
When architects, project managers, and workers all access real-time data, communication flows more smoothly. He adds, “We prioritize collaboration, partnering with global tech leaders such as Oracle, Novade, and OpenSpace to ensure our IoT solutions integrate into the broader project ecosystem.”
With so many technologies at play, owners prefer a unified system where technology providers communicate effectively, streamlining the process from execution to handover. For complex megaprojects, aligning everyone on the same page is crucial for smooth coordination and minimizing errors.
THE TRUE INNOVATION IN PRODUCTIZATION
As productization continues to evolve in urban development, one key innovation in construction technology will be the standardization of data exchange between companies, says Pifko.
As the need for collaboration grows in a productized world, businesses will focus on creating standard ways to share data. He highlights, “Initially, there may be a rush to innovate, but over time, companies will recognize that trade secrets often become commoditized.” As a result, they will standardize the foundational layers of their products while continuing to compete on more advanced or specialized features of their offerings.
Also, balancing standardization with localization involves strategic modular design and adaptive frameworks, adds Alkahlan.
He believes, “The automated production line you aim to implement could adopt a flexible modular design that allows customization based on local cultural, environmental, and architectural requirements.”
While core processes and components are standardized to ensure efficiency and quality, localized variations can be introduced through customizable finishes, designs, and amenities that reflect the unique character of different cities or regions.
For Alkahlan, this approach ensures that even with large-scale production, each community feels personalized and connected to its local heritage.
In addition, embracing advanced digital modeling tools and customer-focused design platforms allows end-users to visualize and participate in the customization process. This participatory design approach promotes a sense of ownership among residents and stakeholders while adhering to overall project efficiency.