- | 4:00 pm
We use 129 billion face masks per month. Now they can be turned into concrete
An Australian lab shows the possibility of diverting face masks and rubber gloves from landfills—and mixing them into concrete.
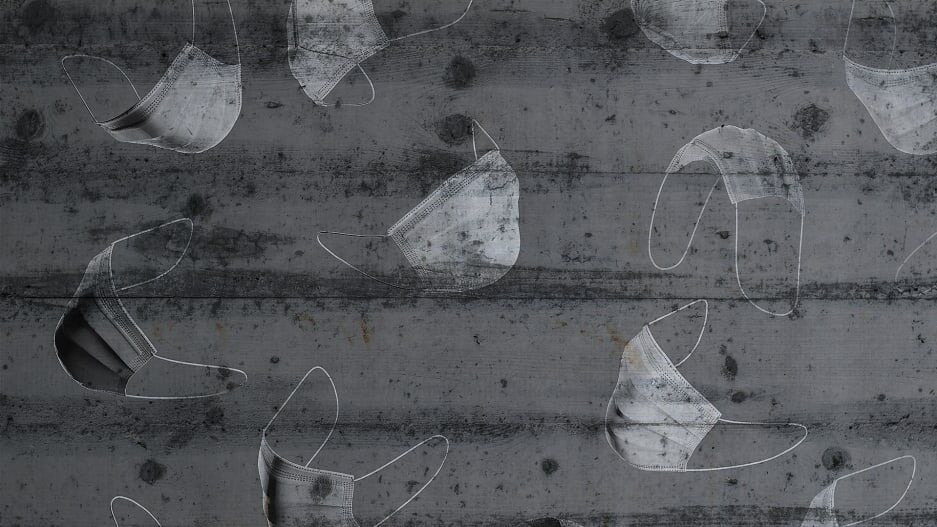
It’s been a difficult balance to strike: protecting communities and healthcare workers from COVID-19 with personal protection equipment (PPE) like face masks, rubber gloves, and isolation gowns—while preventing a waste crisis from the abundance of single-use plastic.
The world has been using 129 billion masks and 65 billion gloves every month since the pandemic’s onset, and an estimated 4.5 trillion masks in 2020 alone. Each day, about 54,000 tonnes of PPE waste travels to landfills, often winding up in the ocean, where sea turtles choke on gloves because they resemble jellyfish, one of their food sources.
Researchers at the Royal Melbourne Institute of Technology (RMIT) in Australia have spent more than a year testing the possibility of reusing PPE—in concrete.
The building material is versatile, but it has poor tensile strength, meaning it can break easily under tension. Reinforcing concrete makes it more durable and more flexible, which the scientists found they could achieve using the plastic in PPE.
They tested masks, gloves, and gowns—each of which is composed of different materials. Nitrile gloves are made of a synthetic rubber polymer; masks contain polypropylene fibers; and gowns have a blend of polyethylene and polypropylene, both plastic polymers (the latter of which can take up to 25 years to break down in a landfill). All three successfully strengthened concrete in testing.
Face masks increased compressive strength by up to 17%; rubber gloves increased compressive strength by up to 22%; and gowns increased compressive strength by 15%, resistance to bending stress by up to 21%, and elasticity by 12%.
The team at RMIT has tested this reinforcement concept in the past. For example, using slag—a stony waste byproduct from refining ores—they developed a zero-cement concrete with high durability (notable because cement is notoriously bad for the environment, representing 4% to 8% of CO2 emissions). They’ve also used recycled tires in concrete to divert solid rubber waste from landfills “and transform it into a valuable resource for the construction industry,” says Shannon Kilmartin-Lynch, research fellow at RMIT and a coauthor of the study, via email.
“PPE is a fibrous material with remarkable properties of high tensile strength and flexibility,” Kilmartin-Lynch says. “When under stress, the fibrous material of the PPE bridges the micro-cracks formed in concrete to increase its strength.”
Kilmartin-Lynch says the process has the potential to scale up for real-world commercial applications. The team is working with Casafico, a sustainable building company in Melbourne, on field trials. They’ve also had interest for possible collaborations from concrete suppliers, local hospitals, and waste management companies.
For safety, so far the tests have been performed using expired PPE rather than waste to avoid the risk of infections from handling used items. But now the team is consulting with medical professionals to determine how best to decontaminate waste items for the process.
At scale, this could provide an extensive solution for curbing PPE waste and, as Kilmartin-Lynch says, make a “valuable contribution to our circular economy.”