- | 3:00 pm
This Danish school is made from straw and seaweed
Bio materials slashed the building’s embodied carbon.
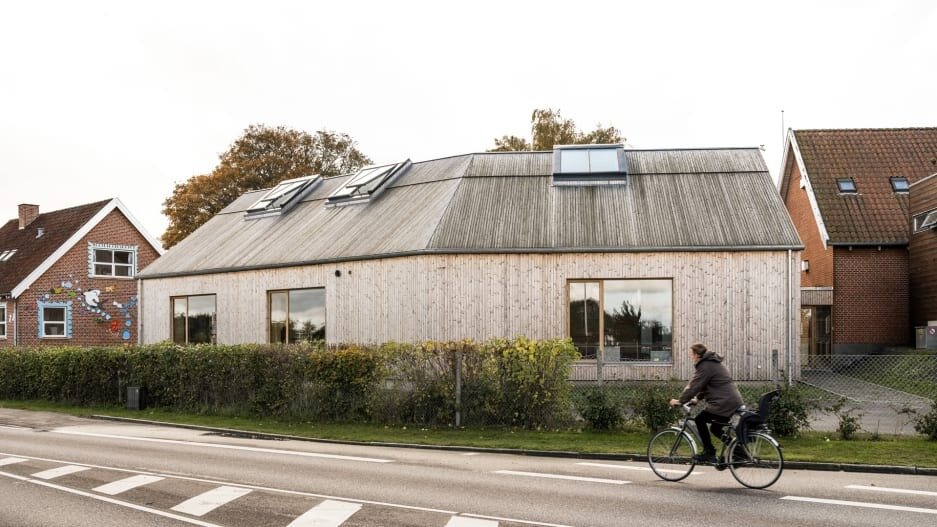
Behind the thick wooden walls of a small school in northern Denmark are two wholly uncommon materials: One is often burned to run the country’s district heating systems. The other usually rots away on the beach.
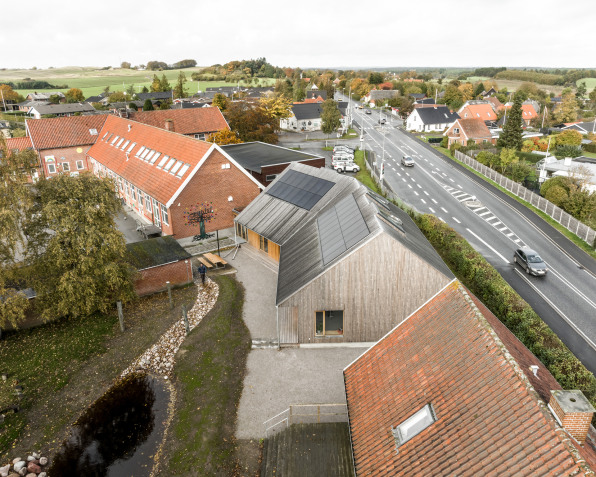
But at the Feldballe School in Rønde, Denmark, Henning Larsen Architects used these two materials—straw and a seaweed called eelgrass—to form the insulation and ventilation systems of a revolutionary kind of building. Designed specifically to reduce the amount of carbon emissions that result from the building’s construction and operable lifespan, the school is showing how biomaterials can help the construction industry hit environmental targets without sacrificing aesthetics.
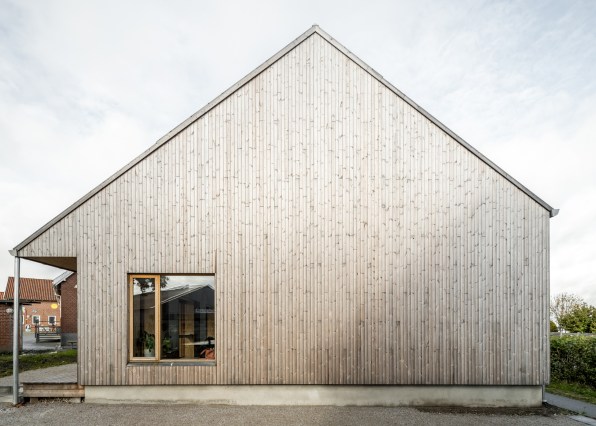
The building is a 2,700-square-foot addition to a school that houses classrooms and science labs. With a wood roof and exterior and its straw walls covered with clay-based plaster, the building is a modern interpretation of a vernacular architecture made from the materials available in the environment. Passively heated and ventilated, its projected annual CO2 emissions will be about half of the level allowed under Denmark’a building code.
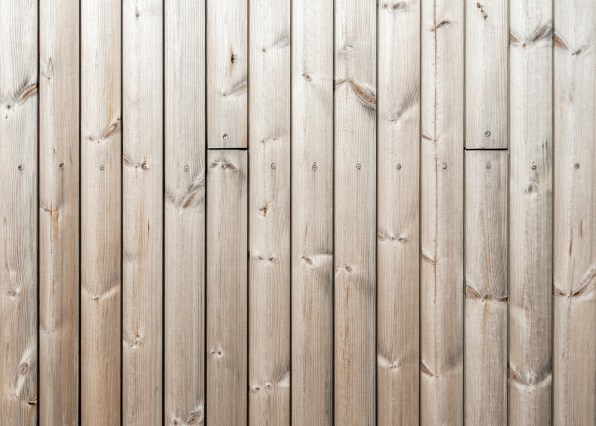
Jakob Strømann is director of sustainability and innovation at Henning Larsen, and he says the idea for using straw came from a PhD student currently working with the Copenhagen-based firm and researching decarbonization. Strømann says building material choices are becoming increasingly important when it comes to reducing the carbon impacts of construction. In Europe, he notes, the electricity grid is becoming greener, so there are fewer carbon reductions to achieve through energy efficiency. Cutting the so-called embodied carbon, or the emissions that come from producing, transporting, and using materials in the construction process, is the new priority. “There’s a shift in balance now,” he says.
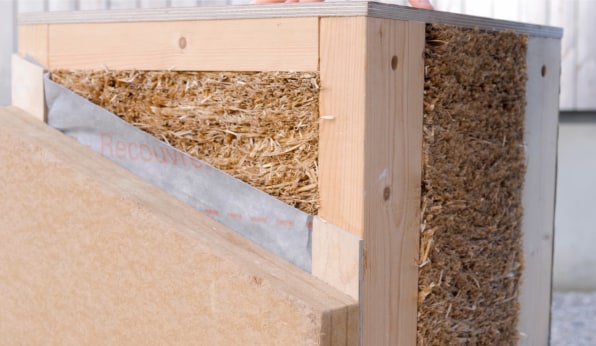
To help target reductions in embodied carbon, the firm created a hierarchy of building materials, modeled after the food nutrition pyramid, with the least carbon intensive at the bottom and the most at the top. “What we found was the best material in the bottom of the pyramid was straw. It has the best absorption of carbon compared to its properties of insulation,” says Strømann. “So, that was the starting point.”
Using hay in buildings is an idea that dates back more than a century. People, especially early environmentalists, have used straw bales as a low cost, low impact, self-built housing construction material since the late 1800s.
Henning Larsen’s design used highly compacted straw as the wall’s insulation, framed by wood for structural support. The firm created some mockups of wall sections in collaboration with a local university’s school of architecture and tested its thermal performance and susceptibility to issues like mold, fire, and even rats.
Henning Larsen then worked with a company called EcoCocon to produce the straw-based wall components. “It was super important for us that it wasn’t some kind of barefoot architecture,” Strømann says. “We want to turn it from a hippie material into an industrial building product.”
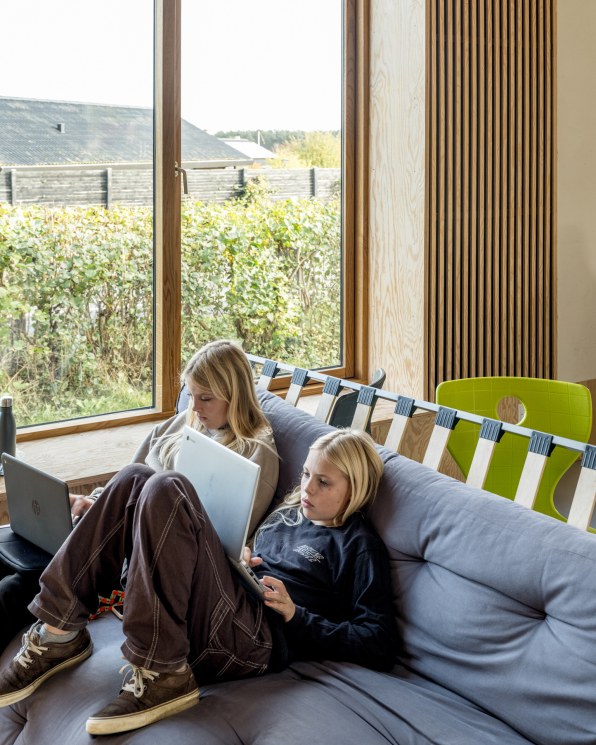
Designed for possible disassembly at the end of its lifespan, the entire school’s building pieces fit onto the back of one truck and were simply bolted together on site. “It was like putting Lego blocks together,” Strømann says.
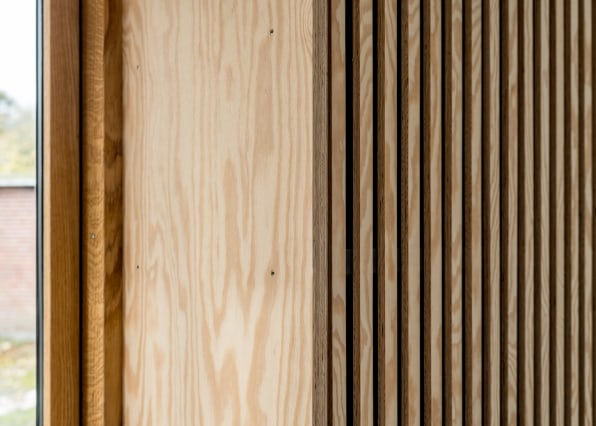
The eelgrass offered another bio-based solution. It washes ashore onto beaches in Denmark, and the plant’s salty content gives it inherent protection from mold and fire, according to Strømann. “You don’t need to put any artificial after-treatments that can create toxicity,” he says. “It’s totally natural, dried by the sun, and inserted as a filter into a passive ventilation unit.”
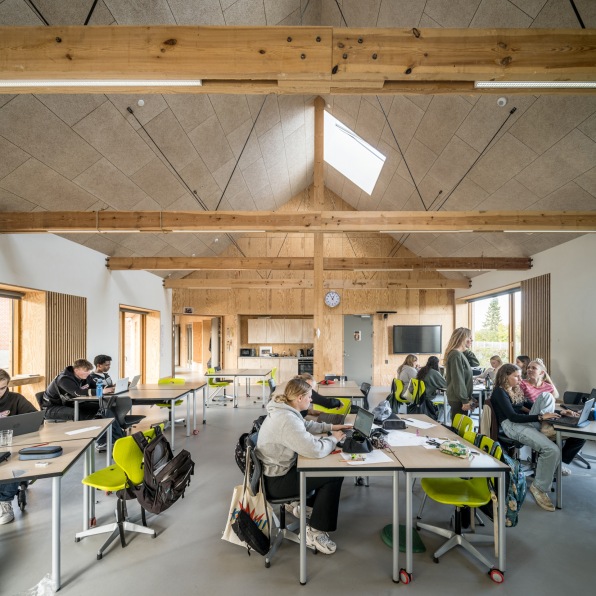
Louvers control the ventilation and keep the school’s classrooms and science labs at steady humidity and carbon dioxide levels. The eel grass vents even help reduce food smells during indoor lunch time.
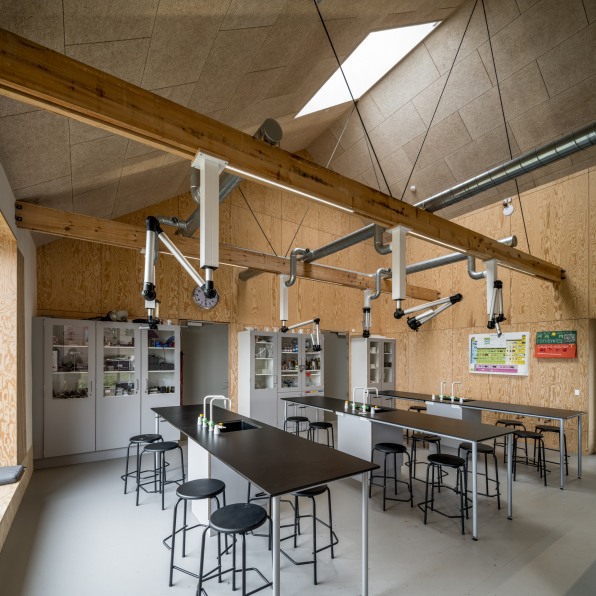
The use of straw for the wall components does have one drawback, though. It’s much thicker than conventional walls, which cuts down on the interior square footage of a building. For this project, a relatively small school addition, the reduction was noticeable if not significant. Strømann says the effect would be diminished in much larger buildings.
And that’s where he sees this leading. The use of a straw-based wall system could be used in warehouses or logistics facilities that typically rely on carbon intensive steel and concrete. “There’s a huge potential,” he says.