- | 8:00 am
This concrete was made from old seashells that trap water and prevent flooding
Researchers have developed a type of concrete that uses discarded shells. It’s now combating floods and food waste in urban gardens and along cycling paths.
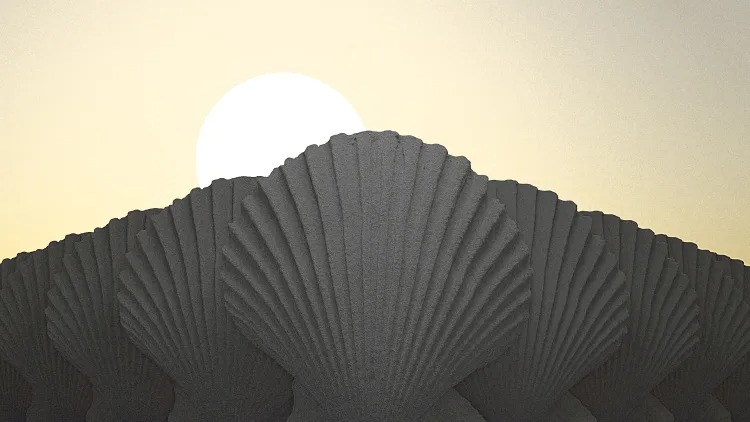
This time of year, bushels of rhubarb, potatoes, and lettuce can be harvested in abundance at the People’s Pantry, a community garden that doubles as a fresh food pantry in Blackpool, England. There, residents living in adjacent affordable housing units tend to the fresh crops they grow and then eat. And lining the ground beneath each raised bed of soil is a smooth sheet of concrete, dotted with slivers of ivory shells.
“They’re not so obvious at first . . . but as you walk on it, the shells become more apparent as you go, and little flecks of white start coming out,” said Helen Jones, operations director at LeftCoast, which runs the local community garden. She’s describing the concrete mix made with crushed seashells that now serves as a sentry against floods for the garden, bolstering the space against stormwater runoff or heavy rains.
It wasn’t too long ago that frequent water inundation was a mainstay at the People’s Pantry. A regular day of rainfall would turn the garden’s corners into something like a marsh, morphing uneven ground into dangerously slick walkways, and even seeping into the housing the land is wedged in between.
This led Jones to meet with local officials last April to see how the issue could be remedied. By the year’s close, the garden’s visitors were looking on in bemusement as a team of scientists at the University of Central Lancashire installed a promising solution: A permeable concrete mix made with cement, aggregate—materials like gravel and rock that are part of typical concrete mixes—and discarded shellfish waste collected from nearby fish processors.
The material is the brainchild of Karl Williams, who directs the Centre for Waste Management at the University of Central Lancashire. His focus on turning items people traditionally perceive to be waste into useful resources is what led him to begin experimenting with using fishing industry shells otherwise tossed into landfills to improve the built environment.
“We’re trying to minimize the carbon footprint of using waste materials, and we’re looking for local solutions,” Williams said.
When crushed, scallop and whelk shells produce an ideal shape that enhances the porosity of pervious concrete, a highly permeable form of concrete, which allows for incoming water to drain right through the layer, instead of amassing on the surface like it would with traditional materials. In coastal, urban environments like Blackpool, where flooding is happening more frequently because of climate change, and an abundance of hard surfaces and a lack of natural greenery means there is a lot more runoff than can currently be absorbed, the shell concrete acts like a sponge, holding onto the water for a period of time before releasing it into the surrounding ground—not unlike a sustainable urban drainage system.
For Williams, the appeal of using discarded seashells to accomplish this flood mitigation is that it also tackles the climate impacts of both food waste and traditional construction. The construction and use of our built environment accounts for more than one-third of global greenhouse gas emissions—the cement industry alone accounts for about 8% of the planet’s carbon emissions—while food waste is responsible for at least another 8%. The climate toll of both industries is what gave Williams the idea to develop the pervious concrete made from locally sourced shells, as part of a European Union-funded multinational research project.
“There’s quite a lot of work around in the construction sector looking at how you can use alternative materials,” said Williams, noting that the construction and food industries happen to be two sectors where “they don’t really talk to each other.” He describes the shell concrete, which he started developing in 2018, as “a conduit for both industries to actually think about the waste that they produce, the products they produce, and how they can work together.”
Fishmongers typically remove the shells from coastal shellfish catches before they sell them to retailers, producers, or directly to consumers. Incorporating them into the concrete material saves them from being simply tossed into landfills, Williams noted. There’s a cost-saving incentive for the fishmongers, too: Currently in the United Kingdom, a shellfish processor looking to dispose of waste shells in landfill must pay almost 100 pounds per metric ton, so Williams says commercial operations have an incentive to avoid contributing to waste and instead give away their garbage to be repurposed.
Meanwhile, the more recycled material that you can put into a building material like cement, the lower the carbon footprint of the production process. Replacing the aggregate with alternative materials can shrink the emissions typically generated from quarrying, processing and transportation.
So far, although the shells added to the concrete mix allow for improved porosity and compressive strength, and decrease the amount of aggregate used by 20% by weight, Williams and his team haven’t quite figured out how to make the overall material carbon-neutral. (Williams says that reducing the emissions footprint of the mixture by investigating lower carbon cements and shell waste processing is the next phase of the project.)
In the research realm, the idea to deploy crushed shells in aggregate solutions to mitigate flood risk is nothing new, and neither is the use of ingredients otherwise destined for landfills in permeable concrete. A 2017 study tested the durability of pervious concrete using crushed seashells, while a 2020 conference paper experimented with crushed coconut shells in building materials, and a 2021 analysis examined oyster shell aggregate for urban greening applications.
But this is one of the first to be used successfully outside of a lab. In addition to the Blackpool community garden, the shell concrete has been laid in a historically flood-prone cycling route in northern France, which Williams’s team worked with multiple organizations to implement in 2022. They are currently in talks to roll this out next at a third test site—a U.K. car park.
“I would not claim this is the very first, or highly innovative, but it’s intriguing, right?” said Xianming Shi, a professor at the University of Miami who studies sustainable construction materials. Shi isn’t convinced that the crushed shell concrete is a large-scale answer to either food waste or emissions associated with concrete. He pointed out that while decomposition of food waste in landfills is a troubling source of emissions, shells don’t contain as much organic waste as other food products, such as fish or vegetables.
He also argued that this material is unlikely to be a primary driver in reducing the emissions of the cement industry, because the use of a recycled material to partially replace aggregate in concrete would not greatly reduce the life-cycle footprint of the concrete, unless this recycled material is carbon negative.
Rather, Shi sees it as an avenue to public engagement with this and other emerging techniques that could eventually make more of a difference. “This type of project, maybe it leads to further interest in unconventional concrete,” he said. Other examples include a living microalgae used to produce bio-cement, developed by researchers at the University of Colorado Boulder, or the work of National Renewable Energy Laboratory scientists to create a lignin-based resin that replaces the cement in concrete.
Some of these may have wider applications than shell-based concrete, which, like other forms of concrete used to absorb flood risk across the world, is riddled with limitations. For one, concrete with high porosity also tends to have lower compressive strength than traditional pavements, meaning it usually isn’t strong enough to act as structural concrete for foundations, nor is it commonly used in high-traffic areas. Many permeable concrete mixtures additionally require regular, specialized maintenance to prevent issues. But while the shell concrete may not function as a large-scale solution, Williams is looking at its use in low-load-bearing sites, such as gardens, parking lots, and sidewalks, where nearby sources of shell waste mean it may be a better answer to flooding woes than other forms of porous concrete.
In a warming world, a seashell concrete may just end up emerging as one among many quick-hit localized solutions in the building and construction industry’s adaptation toolkit.
Williams’s team is now mapping where outside of the U.K. the types of shellfish needed for their concrete can be found to better understand where else this could be tested. Each location poses its own engineering challenges, as different types of shells fracture differently, which matters for the porosity of their product. So what works for an urban garden in Blackpool, England, a seaside town not far from a copious number of cockles and whelks, or a cycling route near French waters where scallops are in no short supply, may not work elsewhere.
More than eight months have passed since the People’s Pantry installed the shell concrete, and Jones says this is their first growing season in years where they haven’t once faced off with a flood. “There’s been no surface water at all,” Jones said. “I mean, we’ve had some quite torrential showers, but you can walk out straight away and there’s nothing being retained.”
And while Jones is enthralled with its multifunctional purpose in reducing the need for concrete aggregate as well as providing a use for food waste (she considers it “brilliant”), visitors to the community garden are often captivated by a much simpler concept: “The residents have a whale of a time just pouring water into it.”
—By Ayurella Horn-Muller, Grist
This article originally appeared in Grist, a nonprofit, independent media organization dedicated to telling stories of climate solutions and a just future. Sign up for its newsletter here.