- | 8:00 am
This beautiful work of art is actually the biggest propeller innovation since the 19th century
The Sharrow CX propeller is proof that engineering is art.
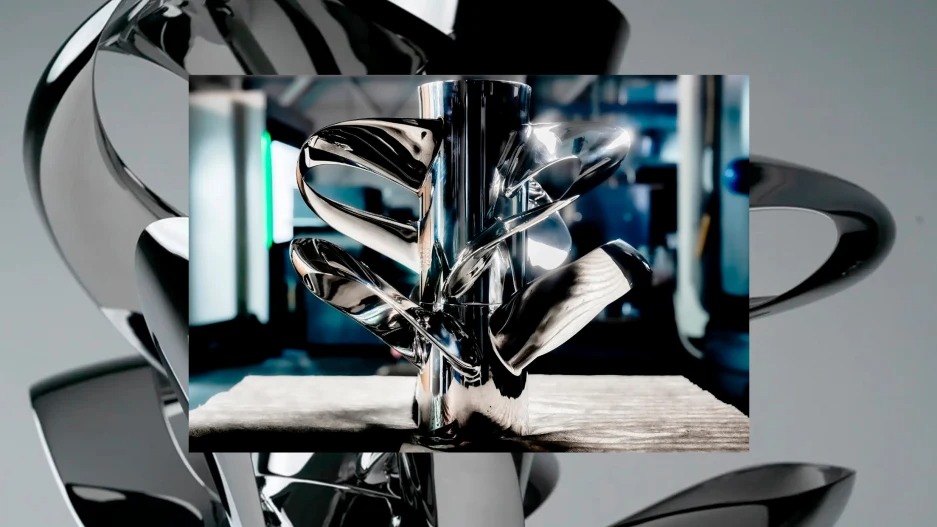
It’s a rare occasion when a piece of engineering transcends its pure industrial function and becomes art. And it’s even rarer when that metamorphosis is the byproduct of a quest for better performance and efficiency. Sometimes, though, math and fluid mechanics produce beautiful things, like nature does.
That’s exactly the case of the Sharrow CX, an object that looks like a glossy sculpture in MoMA’s permanent collection, but is actually something much more mundane: a counter-rotating propeller for boats.
It features a “tipless” design, which means instead of leaving the blade tips free as regular propellers do, the Sharrow CX connects its six blades—which are grouped in two triads—back to the propeller shaft in a smooth, twisted curved surface. The overall design looks like a perfectly metallic gift bow frozen in time.
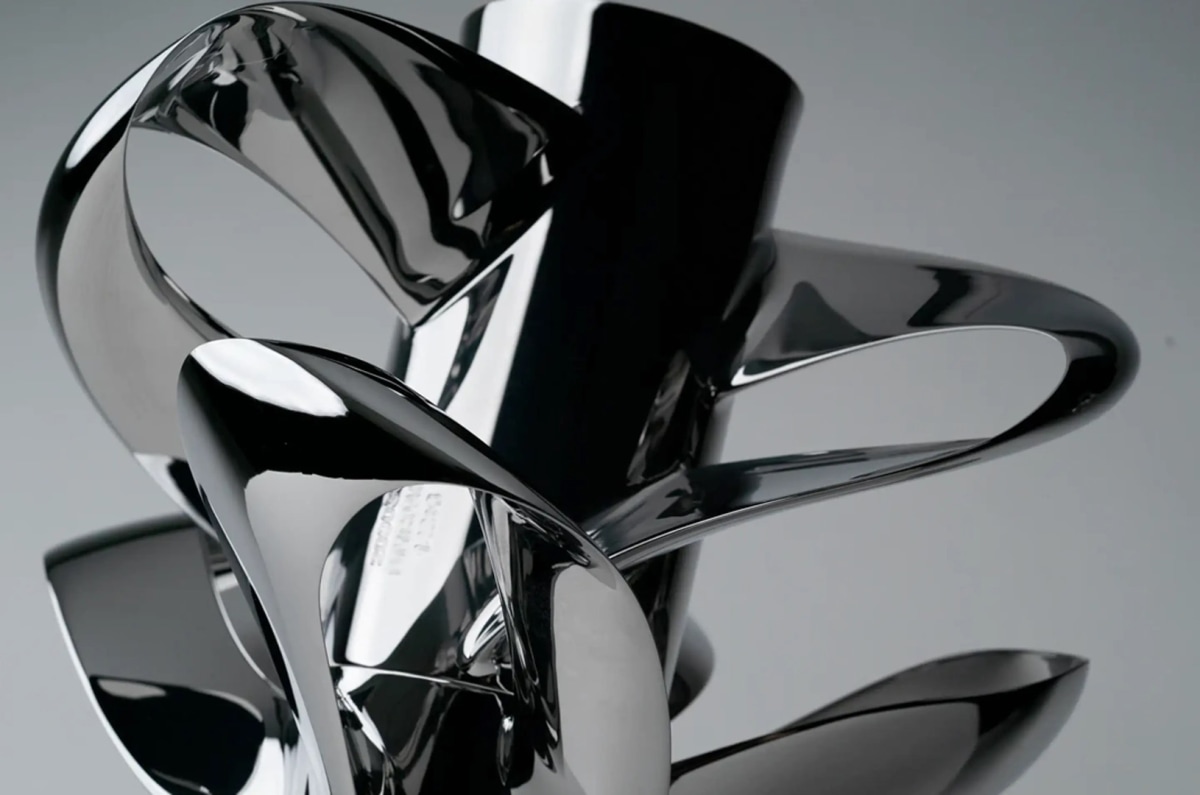
DISCOVERY BY ACCIDENT
Greg Sharrow—founder and CEO of Sharrow Engineering and Sharrow Marine—invented the original Sharrow propeller in 2012. Its genesis, as he tells me via email, is a rather curious one. While working in music production after graduating from Boston’s Berklee College of Music, Sharrow was interested in creating an ultra-quiet drone that he could use in live music performances.
Often, drones create a loud noise that comes from the blades. This is due to something called cavitation, which describes a natural phenomenon that occurs when blades spin at high velocities. At sea, cavitation happens when blade surfaces ‘cut’ through the fluid, creating low-pressure zones that turn into vapor bubbles that pop. The result is the loud noise you can hear on boats equipped with propellers.
Sharrow knew that one of the sources of cavitation are the tips of the propeller’s blades, so he began to experiment with reducing (and ultimately eliminating) the tips through iterative design.
“During the R&D and design process [for the drone propellers], it was faster to do testing in the water because I could manufacture prototype propellers at a much smaller scale due to the increased density of water vs. air,” he explains. Testing them for aerial use would have been much more expensive, and this happy detour to save money and time led to a surprising observation: the tipless folding propeller designs drastically reduced cavitation.
He noticed other clear advantages too: “It results in better performance, improved fuel economy, reduced noise and vibration, and reduced wear and tear on the engine,” he says. A few patents later, Sharrow had what he claims is the first major design change for propellers since the 1830s.

THE NEW CONTRA-ROTATING VERSION
Sharrow’s earlier propeller design (a finalist in the 2023 Innovation by Design awards) rotated the blades go in a single direction. The the new CX propeller, now available for pre-order, has two sets of blades that go in opposite directions.
Other contra-rotating propellers both for marine and aeronautics applications exist, but, according to Sharrow, his company’s special tip-less twisted shape “can harness the torque of a motor more efficiently than standard blades, which is particularly important in situations with contra-rotating propeller blades.” In other words: it uses more of the force created by the engine, thus boosting the fuel efficiency, maneuverability, and reliability of the design. Sharrow says the regular Sharrow design is 30% more fuel-efficient and 80% quieter than standard propellers.
While the company is not sharing exact figures “because these depend on factors such as boat size, engine specifications, and operating conditions,” he told me that rigorous third-party testing has validated the benefits of the Sharrow Propeller in the CX version. He also claims that the new CX version also provides precise handling and maneuvering, even in tight spaces or adverse conditions. “This translates to a smoother, more enjoyable boating experience, with more control of the boat and enhanced safety.”
The company says that the loop-shaped design could be used anywhere, not just in water. “The technology can be used in many applications, including aerospace, aeronautic (drones), HVAC, pumps and renewable energy,” Sharrow says.
THE PROBLEM WITH MANUFACTURING
For now, these propellers seem to have only one problem—they take time to produce. “We are planning to increase manufacturing to 200,000 units per year within the next five years to meet the overwhelming demand we’re experiencing,” he says.
Unlike typical propellers, which are made with molds, Sharrow says that his company uses a proprietary manufacturing method that makes each propeller custom for each boat and motor configuration. “Each propeller is made-to-order, not pulled off the shelf like traditional designs,” he says. “Our application engineers assess model, fit, and performance to select the perfect prop for each customer’s boat and motor combination.” From there, they CNC machine each stainless steel propeller to the customer’s specifications in their Detroit factory. Once the propeller is complete, they have to do a custom fitting to ensure the performance figures.
This high-touch manufacturing method seems to be increasingly more popular and crucial for every industry, especially as we enter the era of AI-driven engineering. I have no boat, and I’m not planning to get one anytime soon, but these are so pretty that I sure would love to have one of them at home, just to marvel at the wonderful beauty of engineering.