- | 9:00 am
These next-gen batteries could be essential to fighting climate change
Companies like Amprius, 6K, Lyten, and ESS are developing new battery technologies to power a greener future.
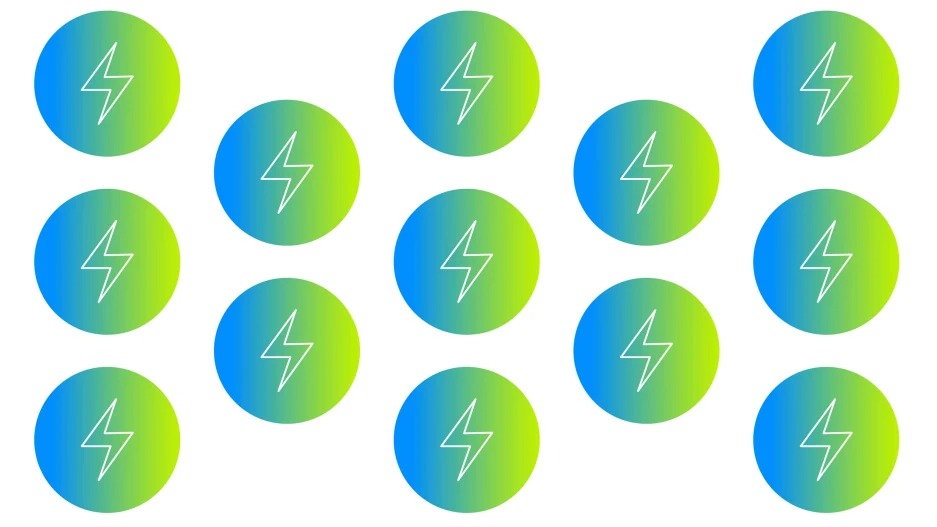
Batteries are hot right now—like really, really hot. Long-lasting, durable, and lightweight storage devices will be an essential part of the global energy transition, yet the tendency of lithium-ion cells to catch fire and explode is only one issue with our most ubiquitous battery technology. A pile of other problems—long charging times, limited life between charges, vulnerability to heat and cold, and the risks around the supply chain of critical metals—has led investors and governments on a billion-dollar quest for the next generation of batteries that can power clean vehicles, complement solar and wind, and keep grids of all sizes resilient. Many of these solutions appear on Fast Company’s 2024 list of the Most Innovative Companies in energy.
For would-be innovators, says Venkat Viswanathan, associate professor of mechanical and aerospace engineering at the University of Michigan, “the question is, which part of the battery should you tackle?” Lithium-ion cells, (first introduced by Sony in 1991), now in all of our phones and cars, aren’t going anywhere soon, and they continue to advance. But their structure presents limitations. A lithium-ion cell consists of two electrodes—a positive cathode and a negative anode—sandwiched around an organic liquid or solid electrolyte; as the battery is charged and discharged, electrically charged lithium ions travel through the electrolyte from one electrode to the other.
Over the past decade, EV companies have upped batteries’ performance and safety with new kinds of cathodes. Now researchers are exploring ways to upgrade the chemistry of the anode. Using a technique developed at Stanford, Fremont, California-based Amprius Technologies replaces the typical graphite anode with a thinner silicon one, producing advantages that could be crucial for transportation and aviation, like the ability to charge from zero to 80% in six minutes or hold a charge long enough to power an overnight stratospheric flight. In October, solar cars powered by its batteries swept the top four places in the Bridgestone World Solar Challenge, the most rigorous solar car race in the world.
In Massachusetts, 6K is rethinking how to make the stuff that goes into all those batteries and more. Using an MIT-born plasma beam that produces temperatures exceeding 6,000 degrees, the company can recycle used metals into almost any lithium-ion battery material, as well as additive powders for 3D printing, in a process that cuts energy use by 70% compared with conventional recycling. With a $50 million grant from the Department of Energy—part of a sweeping effort by the Biden White House to expand homegrown EV batteries—the company is now building a full-scale plant in Jackson, Tennessee. Scheduled to open at the end of 2024, the plant will complement a facility in Pennsylvania that in just three years has become one of the largest battery material factories in the United States.
The transportation industries are also exploring lighter, more powerful lithium-sulfur batteries, which avoid the need for critical materials like nickel, manganese, cobalt, and graphite, and all the carbon costs that come with them. To tame the typically unruly chemistry involved, San Jose-based Lyten makes a “scaffold” of 3D graphene within its batteries. As it scales up its manufacturing ahead of planned shipments this year—to makers of electric vehicles, drones, and satellites—the company is also exploiting 3D graphene as a passive, electronics-free sensing device, useful for monitoring cell safety and performance across a vehicle’s body and tires. (That’s another reason why automaker Stellantis was among a group of big investors that poured $200 million into the company last year.)
In grid storage, where size and weight don’t matter as much, some companies are finding advantages in systems that hardly look like batteries at all. Last September, the Sacramento Municipal Utility District installed a new iron flow battery designed by Oregon’s ESS, which stores energy by circulating liquid electrolytes in tanks that can scale up as needed. Such long-duration storage systems will be essential as utilities across the country zero out carbon and make their grids more resilient to surprises. ESS’s systems last hours longer than conventional lithium-ion systems, without the fire risks or the use of rare earth minerals: the main ingredients are iron, salt, and water.
With similar goals in mind—and the steep cost of repairing the grid after ever more powerful storms—Vermont utility Green Mountain Power is reshaping the grid itself, with a little help from its own customers. Under a newly expanded, first-in-the-country plan, free or discounted home batteries would let customers store power in case of an outage and send it back to GMP to redistribute during peak usage, when traditional energy generation costs are higher, cutting carbon and saving everyone money.
“We’re certainly moving faster,” says Viswanathan, who sees lots of juice in battery innovation and energy storage, which are now top of mind for his students. “The feeling that they’re part of a climate solution—that really drives people.”